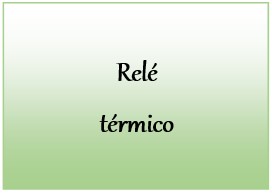
Esquema del Contactor
El esquema del contactor representa gráficamente cómo se conectan sus diferentes partes y cómo funciona dentro de un circuito eléctrico.
El diseño robusto del contactor y su capacidad de manejar altas corrientes lo convierte en un elemento indispensable en muchas instalaciones eléctricas, permitiendo un manejo seguro de la energía eléctrica en todo tipo de aplicaciones.
El esquema eléctrico del contactor permite visualizar de forma clara cómo se conectan los diferentes componentes del contactor (bobina, contactos principales y contactos auxiliares) y cómo interactúan entre sí.
La representación separada del circuito de mando (control de la bobina) y el circuito de fuerza (alimentación de la carga) facilita el diseño y la comprensión de la lógica de control.
El esquema del contactor es uno de los esquemas eléctricos básicos más utilizados gracias a las numerosas ventajas que ofrece este dispositivo que justifican su amplio uso.
Básicamente, el contactor permite controlar circuitos de alta potencia con circuitos de baja potencia, aumentando la seguridad del operador. Además, facilita la automatización de procesos mediante el control de la conexión y desconexión de cargas eléctricas.
Los contactores se diseñan para soportar un gran número de operaciones de conmutación. La gran mayoría se montan sobre carril DIN, que es ampliamente utilizado para el montaje de componentes eléctricos y electrónicos en cuadros eléctricos, armarios de control y otras aplicaciones.
Los contactores están provistos de una pinza o clip en su parte posterior que permite su fijación al carril DIN mediante un simple encaje a presión. Esto facilita enormemente la instalación y el desmontaje de los componentes, ahorrando tiempo y esfuerzo.
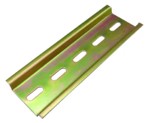
En la siguiente figura se muestra un contactor de la marca “Chint”:
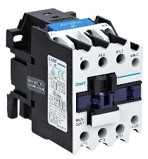
Contenidos
- Qué es un Contactor y para qué Sirve
- Partes de un Contactor
- Funcionamiento del Contactor
- Circuito de Fuerza y Circuito de Mando del Contactor
- Realimentación y Desconexión del Contactor
- Enclavamiento entre Contactores
- Elementos Básicos del Esquema del Contactor
- Esquema del Contactor Monofásico
- Esquema del Contactor Trifásico
- Contactores Auxiliares
- Categorías de Utilización del Contactor
- Aplicaciones del Esquema del Contactor
- Preguntas Frecuentes del Esquema del Contactor
Qué es un Contactor y para qué Sirve
El contactor es un dispositivo electromecánico que se utiliza para abrir o cerrar circuitos eléctricos, ya sea en vacío o en plena carga. Funciona mediante una bobina electromagnética que, al recibir corriente, genera un campo magnético capaz de mover una pieza móvil que activa o desactiva sus contactos eléctricos.
Su principal ventaja radica en permitir el control de grandes cargas con corrientes o tensiones menores, optimizando la seguridad y reduciendo el desgaste de los elementos de mando.
Los usos principales del contactor son:
– Conexión y desconexión de motores eléctricos.
– Control de sistemas de iluminación, calefacción o ventilación.
– Automatización de procesos industriales.
– Protección y control en redes de distribución eléctrica.
Partes de un Contactor
El diseño de un contactor incorpora los siguientes componentes principales:
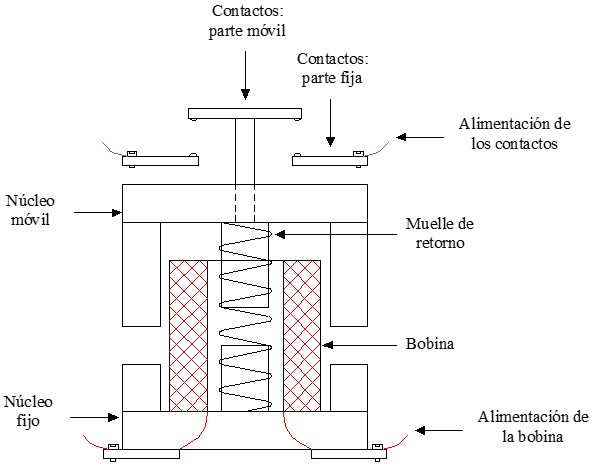
Bobina Electromagnética
Es el elemento actuador del contactor. Al aplicarle un voltaje (tensión de excitación o de mando), genera un campo magnético. Consiste en un arrollamiento de hilo de cobre esmaltado alrededor de un núcleo ferromagnético.
Se alimenta con una tensión específica, que puede ser en corriente alterna (AC) o continua (DC). Las tensiones más comunes son: 24V DC, 24V AC, 110V AC, 230V AC, 400V AC. La elección de la tensión depende del circuito de control. Sus terminales se designan con las letras A1 y A2.
La bobina consume una cierta cantidad de corriente para generar el campo magnético. Este consumo es mayor en el instante inicial de alimentación (corriente de llamada) y disminuye una vez que el contactor está activado (corriente de mantenimiento).
Es muy importante la correcta elección de la bobina según la tensión de control, ya que una tensión incorrecta puede dañar la bobina o impedir su correcto accionamiento.
Núcleo Fijo y Núcleo Móvil
El núcleo fijo y el núcleo móvil forman el circuito magnético del contactor. El campo magnético generado por la bobina atrae el núcleo móvil hacia el núcleo fijo. Están fabricados con material ferromagnético (generalmente acero laminado) para concentrar el campo magnético.
Cuando la bobina se alimenta, el campo magnético atrae al núcleo móvil, que se desplaza hacia el núcleo fijo, cerrando el circuito magnético y provocando el movimiento de los contactos.
Muelle de Retorno
Su función es devolver el núcleo móvil a su posición de reposo (desactivado) cuando la bobina deja de estar alimentada. Es un muelle mecánico que ejerce una fuerza opuesta a la fuerza de atracción magnética.
El muelle tiene gran importancia en el contactor, pues debe tener la fuerza adecuada para asegurar una apertura rápida y segura de los contactos, evitando que estos se queden pegados.
Contactos Principales o de Potencia
Son los contactos que se encargan de conmutar la corriente principal del circuito, es decir, la corriente que alimenta la carga (motor, lámpara, etc.). Están fabricados con materiales conductores de alta calidad (generalmente aleaciones de plata) para minimizar la resistencia y evitar el calentamiento.
Se caracterizan por su capacidad de corriente nominal In, que indica la corriente máxima que pueden soportar de forma continua. La corriente nominal va desde 6 A hasta cientos de amperios.
Los contactores de potencia pueden tener diferentes números de polos (contactos principales), dependiendo de la aplicación. Los más comunes son los tripolares (para circuitos trifásicos) y los unipolares (para circuitos monofásicos).
En un contactor, los contactos principales son siempre contactos de potencia que se cierran cuando se alimenta la bobina del contactor y se abren cuando se elimina la alimentación. Por tanto, se podría decir que son “normalmente abiertos en reposo”.
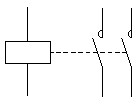
La correcta elección de los contactos principales según la corriente de la carga es fundamental para evitar sobrecalentamientos y daños en el contactor.
Contactos Auxiliares o de Mando
Se emplean para funciones de realimentación del propio contactor, así como para el control, enclavamiento y señalización.
Los contactos auxiliares conmutan cargas de baja corriente. Son similares a los contactos principales, pero de menor tamaño y capacidad de corriente.
Los contactos pueden ser:
● Contactos abiertos (NA): se cierran cuando aplicamos corriente a la bobina.
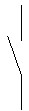
● Contactos cerrados (NC): se abren cuando aplicamos corriente a la bobina.
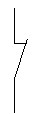
● Contactos conmutados: según la posición del mecanismo alternan entre 2 circuitos diferentes.
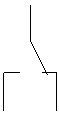
Los contactos auxiliares pueden estar integrados en el contactor, pero también pueden acoplarse en módulos auxiliares.
Los módulos auxiliares también conocidos como bloques de contactos son accesorios compuestos por contactos auxiliares adicionales, que se acoplan a un contactor para aumentar el número de contactos disponibles para maniobra (control y señalización).
Es muy común en aplicaciones donde se utilizan contactores para el control de motores y se necesitan contactos adicionales. Estos bloques no llevan bobina propia, sino que utilizan la bobina del contactor al que están acoplados mecánicamente.
No afectan a los contactos principales del contactor de potencia; solo añaden contactos auxiliares adicionales para incrementar el número de circuitos que se pueden controlar o señalizar con un solo contactor.
Los bloques de contactos se montan directamente sobre el contactor, generalmente en la parte frontal o lateral. El tipo de montaje varía según el fabricante y el modelo del contactor. Algunos se encajan a presión, otros se atornillan.
La conexión eléctrica entre el bloque de contactos y el contactor se realiza de forma interna, a través de un mecanismo que acciona los contactos del bloque simultáneamente con los contactos auxiliares del contactor (si los tiene).
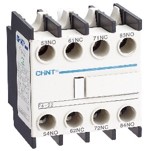
Bornes de Conexión
Los bornes de conexión de un contactor son los terminales donde se conectan los cables para establecer las conexiones necesarias en los circuitos de potencia y control. Suelen ser de tornillo, aunque también los hay de resorte, de inserción rápida, etc.
Estos bornes están organizados en 3 grupos principales: de control, de potencia y auxiliares.
● Bornes de control: controlan el accionamiento de la bobina del contactor. La nomenclatura utilizada para los bornes de conexión de la bobina es A1 y A2:
– A1: se conecta al lado positivo o fase.
– A2: se conecta al lado negativo o neutro.
● Bornes de potencia: conectan las líneas de entrada y salida del circuito de potencia. La nomenclatura es la siguiente:
– L1, L2, L3: bornes de entrada para las fases de la alimentación de corriente alterna (en sistemas trifásicos).
– T1, T2, T3: bornes de salida que alimentan la carga (motores, resistencias, etc.).
En el esquema del contactor, los contactos principales se numeran de acuerdo a las reglas para el marcado de los bornes principales. Por ejemplo, 1-2, 3-4, 5-6 (para contactores tripolares). Esta numeración también suele añadirse junto a los bornes de entrada (L1, L2, L3) y salida (T1, T2, T3).
● Bornes de auxiliares: conectan los cables para funciones específicas en el esquema de mando. Son similares a los contactos principales, pero de menor tamaño y capacidad de corriente.
Los contactores pueden tener diferente número de contactos auxiliares. Se identifican con números de 2 cifras, donde la primera cifra indica el número del contacto y la segunda cifra indica el tipo, siguiendo las reglas para el marcado de los bornes auxiliares. Por ejemplo: 13-14 NA, 21-22 NC.
Funcionamiento del Contactor
El funcionamiento del contactor se basa en el principio de atracción electromagnética:
1º) Alimentación de la bobina: cuando se aplica una tensión a la bobina del electroimán, se genera un campo magnético que atrae al núcleo móvil hacia el núcleo fijo.
2º) Accionamiento de contactos: este movimiento provoca el cierre de los contactos principales, permitiendo el paso de corriente a través del circuito de potencia que alimenta la carga. El movimiento también provoca la maniobra de los contactos auxiliares, cerrando los contactos normalmente abiertos (NA) y abriendo los contactos normalmente cerrados (NC).
3º) Desactivación del contactor: al interrumpir la corriente de la bobina, el campo magnético desaparece, y el muelle de retorno lleva el núcleo móvil a su posición inicial, devolviendo los contactos a su estado de reposo.
El símbolo del contactor engloba todos sus contactos asociados, que dependerán del contactor específico. A continuación, se muestra un contactor trifásico sin neutro con 3 contactos principales y 2 contactos auxiliares, uno normalmente abierto (NA) y otro normalmente cerrado (NC).
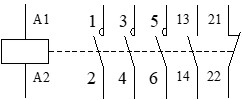
Circuito de Fuerza y Circuito de Mando del Contactor
El circuito de fuerza y el circuito de mando son 2 partes bien diferenciadas de cualquier esquema con contactor. Es importante entender la diferencia entre ambos para comprender cómo opera este dispositivo electromecánico.
Los esquemas de fuerza y de mando se representan por separado buscando priorizar la comprensión del funcionamiento del circuito, más que la representación fiel de su implantación física.
Los dispositivos que disponen de contactos principales y auxiliares, como contactores, relés térmicos y guardamotores, se representan de forma independiente: los contactos principales se dibujan en el circuito de fuerza (que maneja la potencia), y los contactos auxiliares en el circuito de mando (que controla el funcionamiento).
Circuito de Fuerza o de Potencia en el Esquema del Contactor
Este circuito es el encargado de alimentar directamente la carga o receptor eléctrico que se desea controlar (motor, lámpara, resistencia, etc.).
En la siguiente figura, se observa un circuito de potencia, por el que circula la corriente principal que alimenta al receptor, el motor M1.
Los contactos principales del contactor (KM1, 1-2 y 3-4) son los encargados de abrir o cerrar el circuito de potencia. Están diseñados para soportar altas corrientes.
En el circuito de fuerza también se incluyen elementos de protección (Q1) contra sobrecargas, como el relé térmico, y contra sobrecargas y cortocircuitos, como el guardamotor, el fusible o el interruptor automático.
Debido a las altas corrientes que circulan por este circuito, los cables utilizados suelen ser de mayor sección que los del circuito de mando.
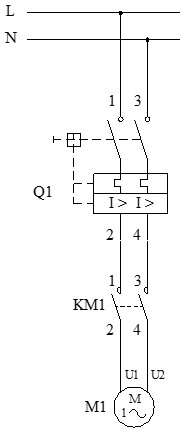
Circuito de Mando o de Control en el Esquema del Contactor
Este circuito es el encargado de controlar la activación y desactivación del contactor.
En la siguiente figura, se muestra un circuito de mando de baja potencia que alimenta la bobina del contactor KM1 (A1-A2).
El circuito debe estar protegido contra sobrecargas y cortocircuitos, siendo los elementos de protección más comunes los fusibles y los interruptores magnetotérmicos (Q2).
Las protecciones del circuito de mando son independientes de las protecciones del circuito de potencia, ya que son circuitos diferentes con necesidades de protección específicas.
Dispone de interruptores y de pulsadores que se utilizan para dar órdenes, como de arranque (pulsador de marcha S2) o de parada (pulsador de paro S1).
También se encuentran contactos auxiliares del contactor, que son contactos adicionales que se abren o cierran simultáneamente con los contactos principales, como el contacto KM1 (13-14). Se utilizan para funciones de autoalimentación (autoenclavamiento), señalización, enclavamientos con otros contactores, etc.
Por último, podemos encontrar otros elementos de control, como relés, temporizadores, finales de carrera, sensores, etc.
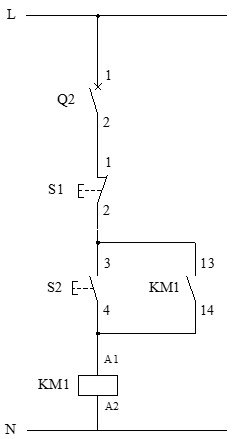
Realimentación y Desconexión del Contactor
Para una comprensión completa del funcionamiento del contactor, es imprescindible conocer 2 conceptos básicos:
● Realimentación o autoalimentación (autoenclavamiento): permite mantener alimentada la bobina del contactor una vez que se ha pulsado y liberado el pulsador S2 de arranque.
Tal y como se observa en la siguiente figura, se logra utilizando un contacto auxiliar normalmente abierto (NA) del propio contactor KM1, que se conecta en paralelo con el pulsador S2 de arranque.
Al cerrar los contactos principales, el contacto auxiliar (NA) del contactor, también se cierra, manteniendo la corriente en la bobina, aunque se suelte el pulsador.
● Desconexión (paro): se basa en interrumpir la corriente que alimenta la bobina del contactor.
El método más común para la desconexión, como se muestra en la figura, es mediante un pulsador S1 de paro normalmente cerrado (NC). Este pulsador se coloca en serie con la bobina del contactor KM1, en el circuito de mando.

Enclavamiento entre Contactores
El enclavamiento entre contactores es una técnica de seguridad en circuitos de control eléctrico que previene la activación simultánea de 2 o más contactores.
Hay casos en los que la activación simultánea de varios contactores genera problemas, como cortocircuitos. Por ejemplo, la inversión de giro de un motor trifásico, la conmutación entre 2 fuentes de alimentación o la conexión directa de 2 fases diferentes a una misma carga.
Existen 2 tipos principales de enclavamiento: eléctrico y mecánico. En aplicaciones críticas o de alta seguridad, se recomienda utilizar ambos enclavamientos (eléctrico y mecánico) para una máxima confiabilidad. Si falla el enclavamiento eléctrico, el mecánico actuará como respaldo, y viceversa.
Enclavamiento Eléctrico entre Contactores
El enclavamiento eléctrico entre 2 contactores impide que ambos se activen simultáneamente previniendo cortocircuitos y daños a los equipos. La idea principal es que si un contactor está activado (enclavado), el circuito del otro contactor se interrumpe, imposibilitando su activación.
El método más común y sencillo es mediante contactos auxiliares normalmente cerrados (NC). Cada contactor utiliza un contacto auxiliar NC que se incluye en el circuito de la bobina del otro contactor.
En la siguiente figura se observa que cuando el contactor KM1 está desactivado, su contacto auxiliar NC está cerrado, permitiendo que la corriente pueda llegar a la bobina del contactor KM2.
Al activar el contactor KM1 mediante el pulsador S2, su contacto auxiliar NC se abre, interrumpiendo el circuito de la bobina del contactor KM2. Incluso si se intenta activar KM2 mediante el pulsador S3, la corriente no podrá circular a través de su bobina.
De forma simétrica, cuando el contactor KM2 está desactivado, su contacto auxiliar NC está cerrado, permitiendo que se pueda activar la bobina de KM1. Al activar KM2, su contacto auxiliar NC se abre, impidiendo la activación de KM1.
Cuando se ha activado un contactor, si se desea activar el otro, se ha de parar previamente el contactor activo, mediante el pulsador de paro S1.
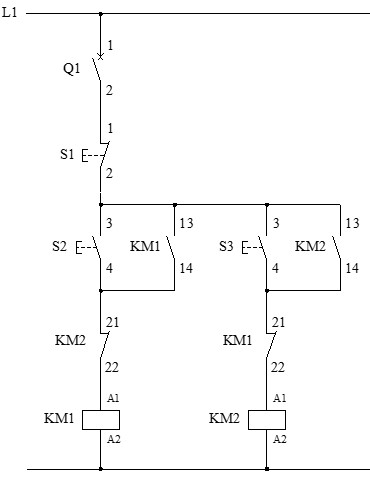
Enclavamiento Mecánico entre Contactores
El enclavamiento mecánico entre 2 contactores es un sistema de seguridad físico que impide la activación simultánea de ambos. El enclavamiento mecánico utiliza un dispositivo físico que bloquea el movimiento de uno de los contactores cuando el otro está activado.
El dispositivo de enclavamiento mecánico consiste generalmente en una pieza que se acopla a los 2 contactores, de tal forma que:
– Cuando un contactor se activa, un brazo o una pieza de bloqueo del enclavamiento se mueve, impidiendo físicamente que el otro contactor pueda cerrar sus contactos.
– Solo cuando el primer contactor se desactiva, el mecanismo de bloqueo se libera, permitiendo que el segundo contactor pueda activarse.
La combinación de ambos enclavamientos, eléctrico y mecánico, ofrece una redundancia que aumenta significativamente la seguridad del sistema.
Los principales casos en los que se recomienda el enclavamiento mecánico adicional son:
● Aplicaciones críticas o de alta seguridad: aplicaciones donde un fallo en el sistema podría tener consecuencias graves. Por ejemplo, maquinaria peligrosa, sistemas de emergencia, ascensores, etc.
● Entornos con vibraciones o golpes: los contactos auxiliares de los contactores pueden verse afectados, lo que podría comprometer el enclavamiento eléctrico.
● Circuitos con alta probabilidad de conmutaciones frecuentes: en circuitos donde los contactores conmutan con mucha frecuencia, el desgaste de los contactos auxiliares aumenta, incrementándose el riesgo de fallo del enclavamiento eléctrico.
● Circuitos con cargas inductivas importantes: las cargas inductivas, como los motores, generan sobretensiones al desconectarse que pueden afectar a los contactos auxiliares y comprometer el enclavamiento eléctrico.
● Cuando se busca la máxima confiabilidad y se quiere minimizar el riesgo de fallos: incluso en aplicaciones no críticas, la combinación de ambos enclavamientos es una buena práctica de ingeniería.
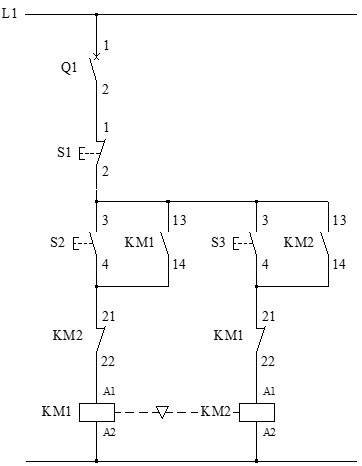
Elementos Básicos del Esquema del Contactor
Para crear un esquema eficiente con contactores, es necesario incluir otros elementos adicionales que permitan funciones, como optimizar el control, garantizar la seguridad y facilitar la operación de las máquinas o sistemas eléctricos a los que están asociados.
Los elementos que podemos encontrar en el esquema del contactor se pueden agrupar en 3 categorías principales: elementos de protección, elementos de maniobra y control, y elementos de señalización.
Elementos de Protección en el Esquema del Contactor
Son elementos que protegen el sistema eléctrico, los equipos y las personas ante condiciones anómalas, como cortocircuitos, sobrecargas, defectos a tierra, fallos en la alimentación, etc. Se utilizan dispositivos como interruptores automáticos, fusibles, diferenciales o dispositivos de protección contra sobretensiones.
Además, hay algunos elementos de protección específicos que se suelen usar para la protección en el esquema del contactor. Se trata del relé térmico o del guardamotor.
Elementos de Maniobra y Control en el Esquema del Contactor
Son los dispositivos que permiten controlar el funcionamiento del contactor, iniciando, deteniendo o controlando el funcionamiento del sistema de automatización. Estos elementos contribuyen a dar las órdenes en el circuito de mando, para activar o desactivar la bobina del contactor y, por tanto, el circuito de potencia.
Las órdenes de maniobra y control pueden ser manuales, a través de la intervención humana, o automáticas, mediante la propia lógica del sistema.
El elemento principal de maniobra es el contactor. Además, en el circuito de mando, operan habitualmente diferentes elementos, como relés electromagnéticos, relés en estado sólido, relés temporizadores y botones pulsadores. Asimismo, puede haber todo tipo de sensores.
Elementos de Señalización en el Esquema del Contactor
Son elementos que informan sobre el estado del sistema, proporcionando retroalimentación visual o auditiva necesaria para la supervisión y el mantenimiento.
Hay diversos tipos de elementos de señalización, siendo los más comunes las lámparas de señalización o los zumbadores.
Esquema del Contactor Monofásico
El contactor monofásico se utiliza específicamente para controlar circuitos eléctricos de corriente alterna monofásica. Al igual que el contactor trifásico, funciona como un interruptor controlado eléctricamente. Por tanto, permite la conexión o desconexión de un circuito de potencia mediante un circuito de control de baja potencia.
Se diferencia del contactor trifásico en que solo dispone de 2 contactos principales: uno para la fase y otro para el neutro.
El contactor monofásico es adecuado para cargas monofásicas como iluminación, calefacción, pequeños motores y otros equipos que operan con una sola fase de la red eléctrica.
El símbolo del contactor monofásico con 2 contactos auxiliares (NA) y (NC) es el siguiente:
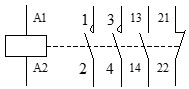
A continuación, se muestra un esquema del contactor monofásico con protección por guardamotor para la maniobra básica de arranque directo de un motor monofásico de CA.
Podemos observar que en el circuito de fuerza se representa el guardamotor Q1, que es un interruptor magnetotérmico con curva térmica regulable y protección a cortocircuitos. Además, también se representan los contactos principales KM1 del contactor.
En el circuito de mando se ha añadido un interruptor automático o disyuntor bipolar Q2 para proteger a sobrecargas y cortocircuitos, y la bobina KM1 del contactor. Asimismo, se puede observar el pulsador S2 de arranque (NA), el contacto auxiliar del contactor KM1 de realimentación (NA) y el pulsador S1 de paro (NC).
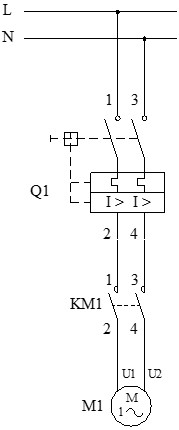
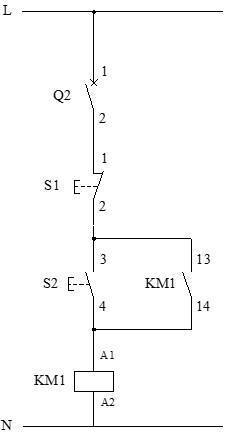
Esquema del Contactor Trifásico
El contactor trifásico es un dispositivo electromecánico diseñado para controlar circuitos de potencia de corriente alterna trifásica. Actúa como un interruptor controlado eléctricamente, permitiendo la conexión o desconexión de un circuito de carga trifásica mediante un circuito de control de baja potencia.
Su principal aplicación reside en el control de motores trifásicos, aunque también se utiliza en otras cargas trifásicas como transformadores, bancos de condensadores y sistemas de iluminación industrial.
Un contactor trifásico generalmente tiene 3 contactos principales, pero también puede tener 4. La diferencia radica en su aplicación y en la necesidad de conmutar el neutro además de las 3 fases.
Esquema del Contactor Trifásico Tripolar
El esquema del contactor trifásico tripolar o de 3 polos se utiliza para conmutar circuitos trifásicos sin neutro. Esta es la configuración más común en la mayoría de las aplicaciones industriales, especialmente para el control de motores trifásicos.
Los 3 polos se encargan de conectar y desconectar las 3 fases de la red eléctrica. En el símbolo del contactor se representan 3 contactos principales, uno por cada fase.
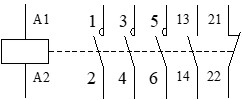
A continuación, se muestra un esquema del contactor trifásico con protección por fusible y relé térmico para la maniobra básica de arranque directo de un motor trifásico de CA.
En el circuito de fuerza, aparte de los contactos principales KM1 del contactor, se utiliza el relé térmico F1, cuya función es proteger al motor frente a sobrecargas, regulándose a la intensidad nominal del motor. Por otro lado, los fusibles Q1 se utilizan para proteger al motor frente a cortocircuitos utilizándose fusibles tipo aM.
El circuito de mando se protege mediante un interruptor automático (disyuntor) bipolar Q2. Se utilizan pulsadores de paro y marcha, así como realimentación o enclavamiento del contactor KM1.
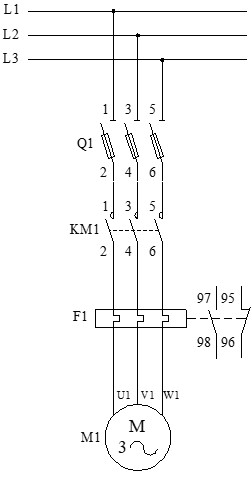
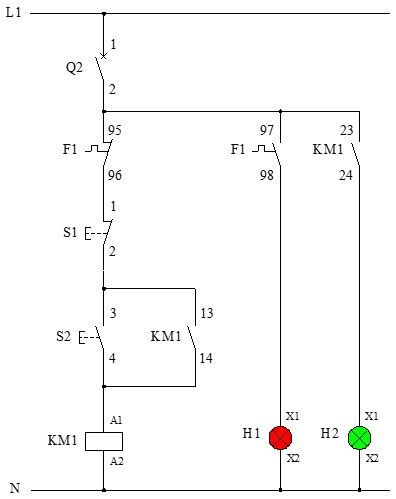
Además, en el circuito de mando se han dispuesto 2 lámparas de señalización:
– Lámpara roja (H1): se enciende cuando el relé térmico F1 detecta una sobrecarga en el motor mediante el contacto NA de este relé.
– Lámpara verde (H2): se enciende cuando el motor está en marcha en condiciones normales. Preferiblemente se señaliza mediante un contacto auxiliar del contactor KM1, aunque también puede hacerse conectando la lámpara en paralelo con la bobina del contactor.
Esquema del Contactor Trifásico Tetrapolar
El esquema del contactor trifásico de 4 contactos principales es útil en aplicaciones donde se requiere la conmutación y control simultáneo de 3 fases (L1, L2, L3) y el neutro (N).
Las aplicaciones comunes de los contactores tetrapolares son en sistemas eléctricos trifásicos, con receptores trifásicos o monofásicos, donde el uso del neutro es indispensable para el funcionamiento adecuado de los receptores conectados.
Esto es común en algunos motores trifásicos que necesitan el neutro para conectar componentes auxiliares. Por ejemplo, en instalaciones de iluminación industrial o alumbrado público con lámparas alimentadas por diferentes fases, en hornos eléctricos industriales, en sistemas de calefacción eléctrica, en conmutación de fuentes de alimentación de reserva, etc.
En el símbolo del contactor se representan 4 contactos principales, 3 para las fases y 1 para el neutro.
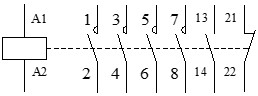
A continuación, se muestra un esquema del contactor trifásico tetrapolar para la alimentación de un conjunto de lámparas monofásicas que necesitan el neutro.
En el circuito de fuerza, están los contactos principales KM1 del contactor que alimenta a las lámparas. Además, hay un interruptor automático Q1 que protege el circuito de sobrecargas y cortocircuitos, más un interruptor diferencial Q2 que protege contra corrientes de defecto a tierra.
El circuito de mando queda protegido mediante un interruptor automático (disyuntor) bipolar Q3. Se utilizan pulsadores de paro S1 y marcha S2, así como realimentación o enclavamiento del contactor (contacto NA auxiliar de KM1).
También se ha dispuesto una lámpara H1 de señalización conectada en paralelo con la bobina del contactor que señalará el encendido de las lámparas E1, E2 y E3 del circuito de iluminación.
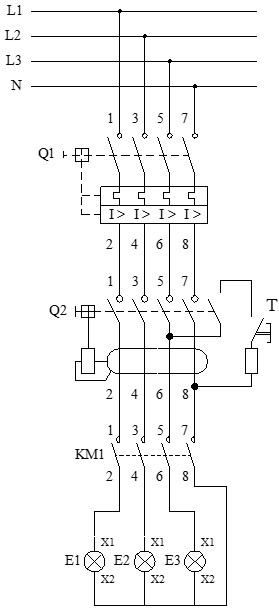
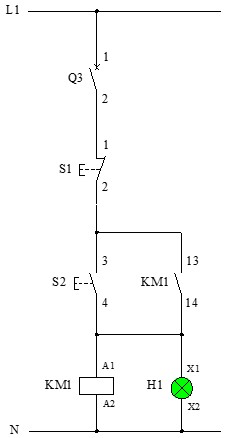
Para el control del alumbrado público, se utilizan frecuentemente contactores tetrapolares. La activación de este contactor se realiza mediante una fotocélula o mediante un interruptor horario que alimenta la bobina KM1 del circuito de mando.
Contactores Auxiliares
Un contactor auxiliar, también conocido como relé auxiliar o relé de maniobra, es un dispositivo electromagnético similar a un contactor, pero diseñado específicamente para el control de circuitos de baja potencia.
La diferencia fundamental es que carece de contactos de potencia, es decir, no conmuta directamente cargas de alta corriente como motores u otras cargas de gran consumo. Su función se centra en la maniobra, el control y la señalización dentro de un circuito eléctrico.
Al igual que el contactor, dispone de una bobina que, al ser alimentada, provoca el cierre (o la apertura) de contactos eléctricos. Físicamente, se asemejan a los contactores de potencia de menor tamaño, compartiendo incluso el mismo tipo de montaje (carril DIN).
El contactor auxiliar solo posee contactos auxiliares. Estos contactos conmutan corrientes pequeñas, del orden de amperios o incluso miliamperios, y se utilizan para:
● Señalización: indicar el estado de un circuito (ej: encendido/apagado de un motor, activación de una alarma).
● Realimentación o autoenclavamiento: mantener un circuito activado incluso después de que haya desaparecido la señal de activación inicial.
● Enclavamiento entre contactores: evitar que 2 contactores trabajen simultáneamente en configuraciones como el arranque estrella-triángulo o el inversor de giro.
● Adaptación de niveles de tensión: adaptar niveles de tensión entre diferentes partes del circuito de mando. Por ejemplo, un detector con salidas de 12V DC puede controlar un circuito que opera a 230V AC utilizando un relé auxiliar con una bobina de 12V DC y contactos que soporten 230V AC.
Los contactores auxiliares también pueden tener diferentes configuraciones de contactos, como normalmente abiertos (NA), normalmente cerrados (NC) o contactos conmutados (o de 3 vías).
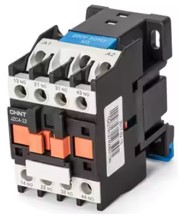
Categorías de Utilización del Contactor
Las categorías de utilización de los contactores, definidas en la norma IEC 60947-4-1 (Aparamenta de baja tensión. Parte 4-1: Contactores y arrancadores de motor. Contactores y arrancadores electromecánicos), clasifican a los contactores según el tipo de carga que controlan y las condiciones de servicio.
La norma define 4 categorías de uso, para corriente alterna, AC1, AC2, AC3 y AC4 según la carga y las funciones de control ofrecidas por el contactor. Para corriente continua define 3 categorías, DC1, DC3 y DC5.
Contactor de Categoría AC-1
Se aplica a cargas puramente resistivas o ligeramente inductivas, donde la corriente de arranque no es significativamente mayor que la corriente nominal.
La corriente de conexión es baja y la corriente de corte es igual a la corriente nominal. El contactor no sufre un estrés eléctrico significativo durante la conexión y desconexión.
Ejemplos de aplicación: cargas de calefacción resistivas, hornos, iluminación incandescente.
Contactor de Categoría AC-2
Esta categoría se aplica al arranque, la conexión y el avance lento de motores de inducción con rotor bobinado (anillo rozante).
Deben soportar alta corriente inicial durante el arranque, con la necesidad de soportar la desconexión en condiciones de corriente elevada, así como las maniobras de frenado a contracorriente.
Ejemplos de aplicación: motores para grúas o montacargas.
Contactor de Categoría AC-3
Esta categoría se aplica a los motores de inducción de jaula de ardilla (rotor en cortocircuito) durante el funcionamiento normal del motor. Se aplica al arranque y a la desconexión del motor una vez que ya está en marcha.
El contactor debe ser capaz de soportar la corriente de arranque, que puede ser de 5 a 8 veces la corriente nominal del motor. Debe soportar también la corriente nominal durante el funcionamiento y la desconexión en condiciones de corriente nominal.
Ejemplos de aplicación: ascensores, escaleras mecánicas, cintas transportadoras, elevadores de cubos, compresores, bombas, mezcladores, unidades de aire acondicionado, etc.
Contactor de Categoría AC-4
Esta categoría se aplica a los motores de inducción de jaula de ardilla (rotor en cortocircuito) para el arranque, frenado a contracorriente e impulsos.
Esta es la categoría más exigente para los contactores. Además de soportar las altas corrientes de arranque (como en AC-3), debe soportar las corrientes generadas durante el frenado a contracorriente y las maniobras de impulsos (conexiones y desconexiones frecuentes).
Ejemplos de aplicación: máquinas de elevación (grúas), máquinas herramienta, prensas, etc. También en aplicaciones donde se requieren arranques y paradas frecuentes o un control preciso de la posición.
Categorías de Contactores para Corriente Continua
Las 3 categorías para contactores de corriente continua son:
● Categoría DC-1: para cargas puramente resistivas o ligeramente inductivas. Requiere contactos de alta capacidad para manejar corrientes sin efectos inductivos. Por ejemplo, resistencias calefactoras en corriente continua.
● Categoría DC-3: para arranque, parada y marcha atrás de motores en derivación de corriente continua. Manejo de corriente elevada al arranque y conmutación frecuente bajo carga. Por ejemplo, motores para grúas o elevadores.
● Categoría DC-5: para arranque y parada de motores en serie de corriente continua. Requiere capacidad para soportar alta corriente al arranque y conmutación frecuente. Por ejemplo, tracción eléctrica, maquinaria pesada.
Aplicaciones del Esquema del Contactor
La capacidad del contactor para manejar altas corrientes y tensiones lo convierte en un componente esencial en sistemas eléctricos industriales y comerciales:
– Control de motores eléctricos: para arranque y paro de motores trifásicos o monofásicos, para inversión de giro de motores y para arranque suave en combinación con resistencias o autotransformadores.
– Iluminación interior y exterior: permiten el encendido y apagado de alumbrado público desde un sistema de control centralizado. Facilitan la gestión de luminarias de alto consumo, como las utilizadas en almacenes, estadios y fábricas.
– Automatización industrial: controlan máquinas y equipos en líneas de producción. Mediante temporizadores y relés auxiliares, los contactores sincronizan el funcionamiento de diversos dispositivos. Además, en sistemas modernos, los contactores son accionados por controladores lógicos programables (PLCs).
– Sistemas de calefacción y climatización: en sistemas de calefacción industrial, los contactores manejan corrientes elevadas generadas por resistencias calefactoras. También permiten activar compresores y ventiladores en grandes instalaciones de climatización.
– Sistemas de compensación de energía reactiva: en instalaciones industriales, los contactores regulan la conexión de condensadores. Así, se mejora el factor de potencia y se reducen penalizaciones.
– Gestión de equipos eléctricos de alta potencia: controlan la alimentación de sistemas de bombeo y compresión de tornos, así como fresadoras y otras máquinas de taller.
– Energías renovables: gestionan la conexión entre paneles solares, inversores y la red eléctrica. En sistemas eólicos controlan la conexión de turbinas eólicas a la red en sistemas de almacenamiento de energía.
– Sistemas de transferencia automática (ATS): en sistemas de respaldo, los contactores gestionan el cambio automático entre la red principal y generadores auxiliares.
– Aplicaciones en minería y transporte: operan equipos de minería, como cintas transportadoras y excavadoras eléctricas. En sistemas ferroviarios permiten la gestión de circuitos eléctricos en trenes y tranvías.
Preguntas Frecuentes del Esquema del Contactor
También te puede interesar:
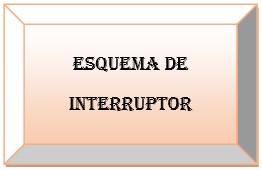
Esquema de Interruptor
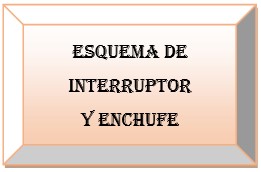
Esquema de Interruptor y Enchufe

Esquema de Doble Interruptor
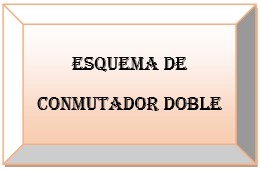
Esquema de Conmutador Doble
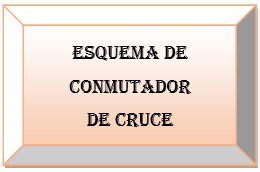
Esquema de Conmutador de Cruce
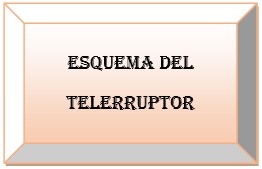
Esquema del Telerruptor
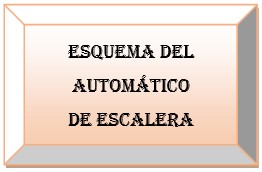
Esquema del Automático de Escalera
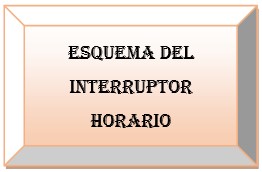
Esquema del Interruptor Horario
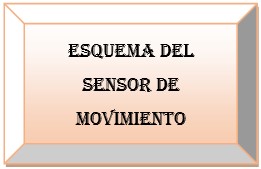
Esquema del Sensor de Movimiento
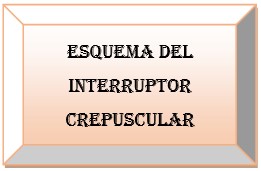
Esquema del Interruptor Crepuscular
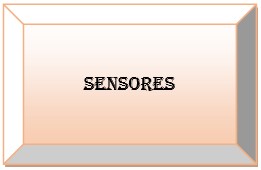
Sensores
-
Excelente para enseñar a los alumnos de 2° año escuela técnica claro directo y específico. Muchas gracias
★★★★★
-
Excelente, muchas gracias!
★★★★★
Deja una respuesta
exelente documento
★★★★★